In this article, I will explore the different categories of knife steel, their properties, and how to choose the right steel for your needs.
There are three main types of knife steel: high toughness, balanced, and high wear resistance. Each category serves different purposes and offers unique advantages, which I’ll explain in detail.
๐High Toughness Steels
High toughness steels are designed to withstand significant impact and stress without chipping or breaking. These steels are perfect for situations where you need something very durable that won’t break easily under heavy use. Great examples of high toughness stainless steels are AEB-L and 14C28N.
AEB-L and 14C28N
Both AEB-L and 14C28N originate from Sweden and were initially developed for razors. The primary goal was to create a steel with a super fine microstructure that could achieve extremely sharp edges for shaving.
This fine microstructure is crucial because, under a microscope, a razor’s edge must be smooth and sharp to prevent discomfort and skin irritation. This attribute makes these steels excellent for a wide range of applications, from razors to large chopping tools.
AEB-L is known for its excellent toughness and ability to take a fine edge. It is often compared to 440A, an older steel with a similar carbon content. However, AEB-L’s design and optimized processing for razors set it apart, providing much higher toughness and a finer microstructure.
14C28N, on the other hand, builds on the properties of AEB-L by incorporating nitrogen into its composition. This modification enhances its corrosion resistance while maintaining the same level of toughness and fine edge retention.
As a result, 14C28N can be considered an upgrade over AEB-L, offering better overall performance.
Applications and Heat Treatment
These high toughness steels can be used in various tools, from large choppers to delicate razors. The key to optimizing their performance lies in the heat treatment process.
For large choppers, a lower hardness level is preferred to enhance toughness, while for razors, a higher hardness level is necessary to maintain a sharp, thin edge without rolling.
This versatility makes high toughness steels a popular choice among knife makers and users.
๐Balanced Steels
Balanced steels offer a well-rounded combination of properties, making them suitable for a wide range of applications. They provide a good balance of toughness, wear resistance, and corrosion resistance.
Top choices in this category include CPM 154, S35VN, and MagnaCut.
CPM 154 and S35VN
CPM 154 and S35VN are powder metallurgy stainless steels known for their balanced properties. Powder metallurgy involves producing steel from powdered metals, resulting in a finer and more uniform microstructure. This process enhances the steel’s overall performance.
CPM 154 is praised for its excellent corrosion resistance, good wear resistance, and toughness. It is a popular choice among custom knife makers due to its ease of finishing and versatility.
S35VN, an evolution of the popular S30V, includes niobium in its composition, which improves its toughness and ease of sharpening while maintaining high wear resistance. This steel is widely used in high-end knives and is favored by many knife enthusiasts.
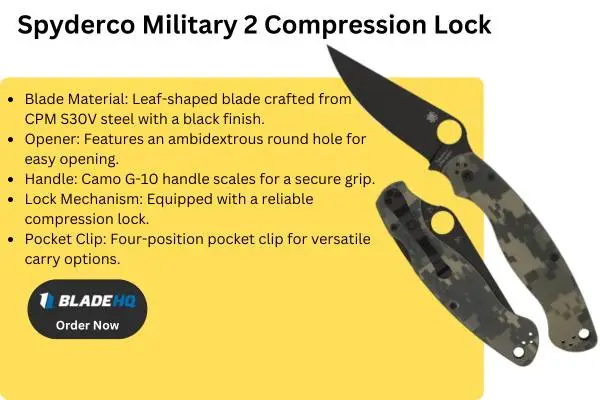
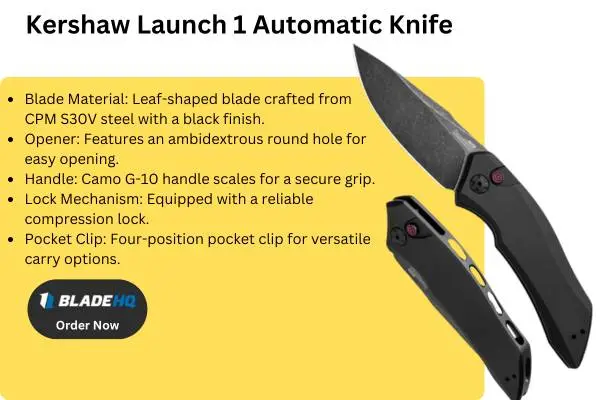
MagnaCut: The New Standard
MagnaCut is a relatively new addition to the balanced steel category, which was designed to address the limitations of existing steels while enhancing their strengths. MagnaCut offers a remarkable balance of properties, including high toughness, excellent wear resistance, and superior corrosion resistance.
One of the key advantages of MagnaCut is its versatility. It can be heat treated to achieve a wide range of hardness levels, from 64-65 HRC for small batches to lower hardness levels for more toughness. This flexibility allows MagnaCut to be used in various applications, from large competition choppers to thin kitchen knives.
Custom Knife Making Considerations
While MagnaCut and other balanced steels offer excellent properties, they present some challenges for custom knife makers.
The presence of vanadium and niobium carbides in these steels makes them harder than conventional abrasives, making finishing by hand more difficult.
Custom knife makers often need specialized techniques and tools to achieve the desired finish. Despite these challenges, the performance benefits of balanced steels make them a worthwhile choice for many knife makers.
๐High Wear Resistance Steels
High wear resistance steels excel in edge retention, especially for slicing tasks. These steels are designed to withstand prolonged use without losing their sharpness. Prime examples of high wear resistance steels are S90V and S110V.
S90V and S110V
Both S90V and S110V are powder metallurgy steels with high vanadium content. Vanadium carbides contribute to their exceptional wear resistance, allowing these steels to maintain a sharp edge for extended periods.
S90V is known for its excellent balance of wear resistance and toughness. It offers high edge retention while still providing reasonable toughness for demanding tasks.
S110V takes wear resistance to the next level, surpassing S90V in this regard. However, it sacrifices some toughness compared to S90V. Despite this trade-off, S110V’s wear resistance makes it a top choice for applications where edge retention is paramount.
Applications and Considerations
High wear resistance steels are ideal for tasks that involve repetitive slicing and cutting, such as kitchen knives and certain types of outdoor knives. Their ability to retain a sharp edge over time reduces the need for frequent sharpening, making them convenient for users who require long-lasting performance.
However, the high wear resistance of these steels also means they can be more challenging to sharpen when they do eventually dull. Users may need diamond or ceramic sharpeners to effectively maintain the edge. Despite this, the benefits of high wear resistance steels in terms of longevity and cutting performance make them a valuable choice for specific applications.
Edge Geometry is Very Important
While the choice of steel is crucial, edge geometry plays an even more significant role in a knife’s performance. The angle and shape of the edge can greatly impact cutting efficiency, durability, and overall performance.
Optimizing Edge Geometry
Edge geometry refers to the angle and shape of the blade’s edge. A more acute angle (sharper) can provide better cutting performance but may be more prone to chipping or rolling. Conversely, a more obtuse angle (blunter) increases durability but may reduce cutting efficiency.
For optimal performance, users should tailor the edge geometry to the specific cutting tasks they intend to perform. For example, a kitchen knife used for slicing vegetables may benefit from a more acute angle, while a heavy-duty outdoor knife may require a more obtuse angle for added durability.
Impact of Edge Geometry on Steel Performance
Research and testing have shown that edge geometry can have a more significant impact on a knife’s performance than the choice of steel or heat treatment. A knife with optimized edge geometry can outperform higher-end steels if the geometry is tailored to the intended use.
For instance, in one test, CPM 154 outperformed S90V simply by adjusting the edge angle. This finding highlights the importance of understanding and optimizing edge geometry to maximize a knife’s performance.
Conclusion
Choosing the best knife steel depends on understanding the different categories and their specific properties. High toughness steels like AEB-L and 14C28N offer excellent durability and fine edges, making them versatile for various applications.
Balanced steels such as CPM 154, S35VN, and MagnaCut provide a well-rounded combination of toughness, wear resistance, and corrosion resistance, suitable for a wide range of uses.
High wear resistance steels like S90V and S110V excel in edge retention, making them ideal for tasks that require prolonged sharpness.
In addition to selecting the right steel, optimizing edge geometry is crucial for maximizing a knife’s performance. By tailoring the edge angle and shape to the intended cutting tasks, users can significantly enhance their knife’s efficiency and durability.
For those looking to dive deeper into the world of knife steels and edge geometry, the book “Knife Engineering” by Dr. Larrin Thomas, offers a comprehensive guide with detailed explanations and practical insights. Additionally, the website Knife Steel Nerds is a valuable resource for anyone interested in learning more about the science behind knife steels.